Manufacturers are always looking for ways to increase their productivity. To be able to do this firstly you need a system that records and reports on your losses, the Six Big Losses model as below is the foundation for this.
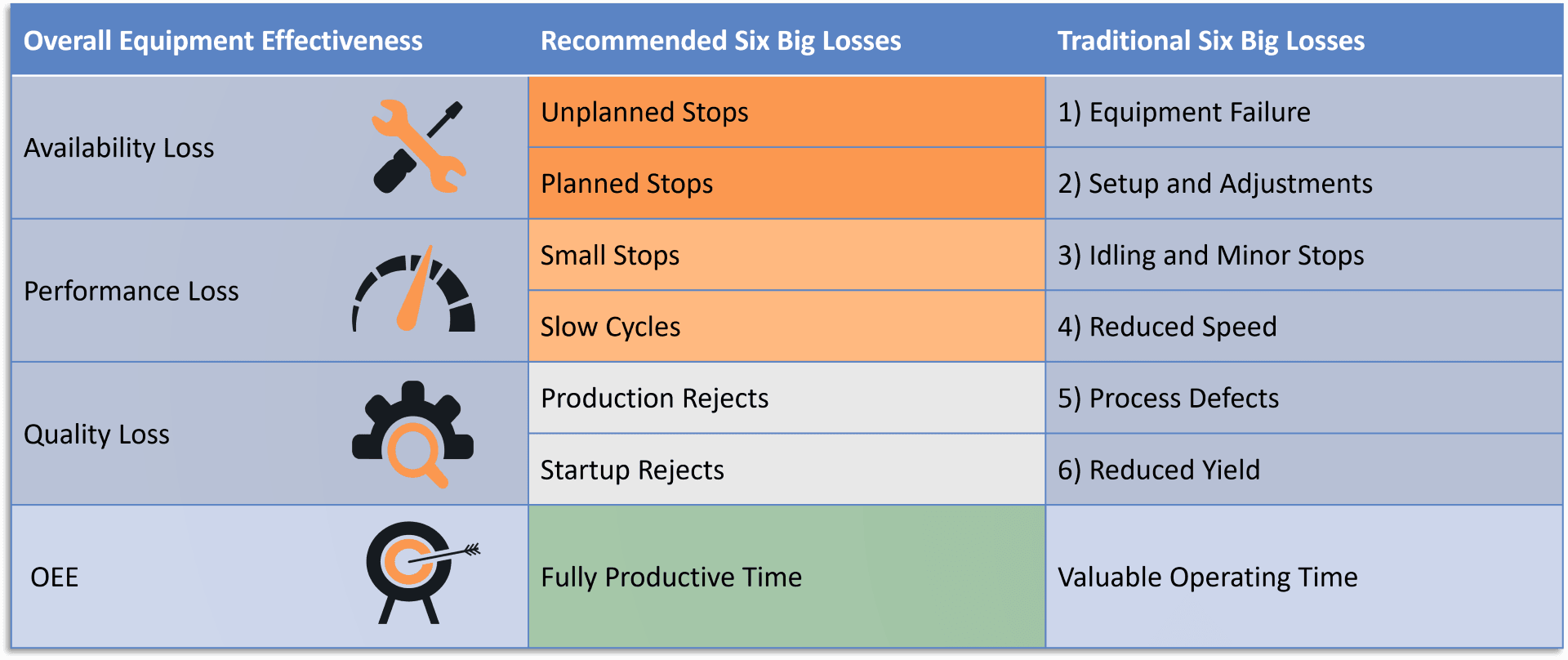
The Six Big Losses. Source: OEE.com
Most manufacturers will use OEE (Overall Equipment Effectiveness) as a key measure of their shopfloor efficiency and performance, the recording of downtime and speed loss, along with production yields and scrapping is key to the calculation. It’s important when defining the categories they are simple but detailed enough for reporting and analytics as well as understood by the operators. For example, if you have too many categories, operators may be confused or have differing opinions on which categories to use, this in turn dilutes or even obscures the reporting and therefore lessens the ability to improve and understand what changes will have the biggest impact.
So what is OEE?
If you understand what OEE is then skip this section and jump right into "Accessing the Financial Impact of Improving Your OEE" but for those that don’t or need a refresher here is a simple introduction to OEE.
In a nutshell OEE measures the percentage of planned production time that was productive and free of defects.
The metric of OEE is the adopted benchmarking tool and forms a framework for understanding your production and the areas for improvement.
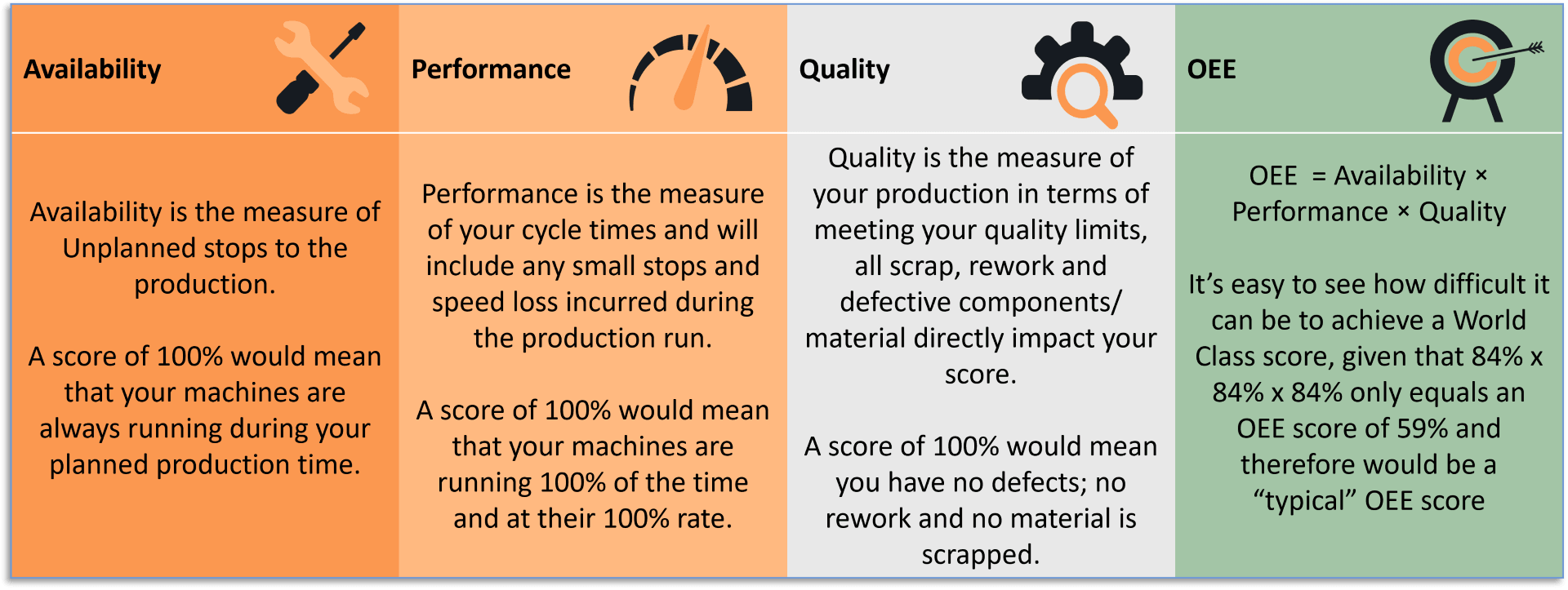
What does Good look like?
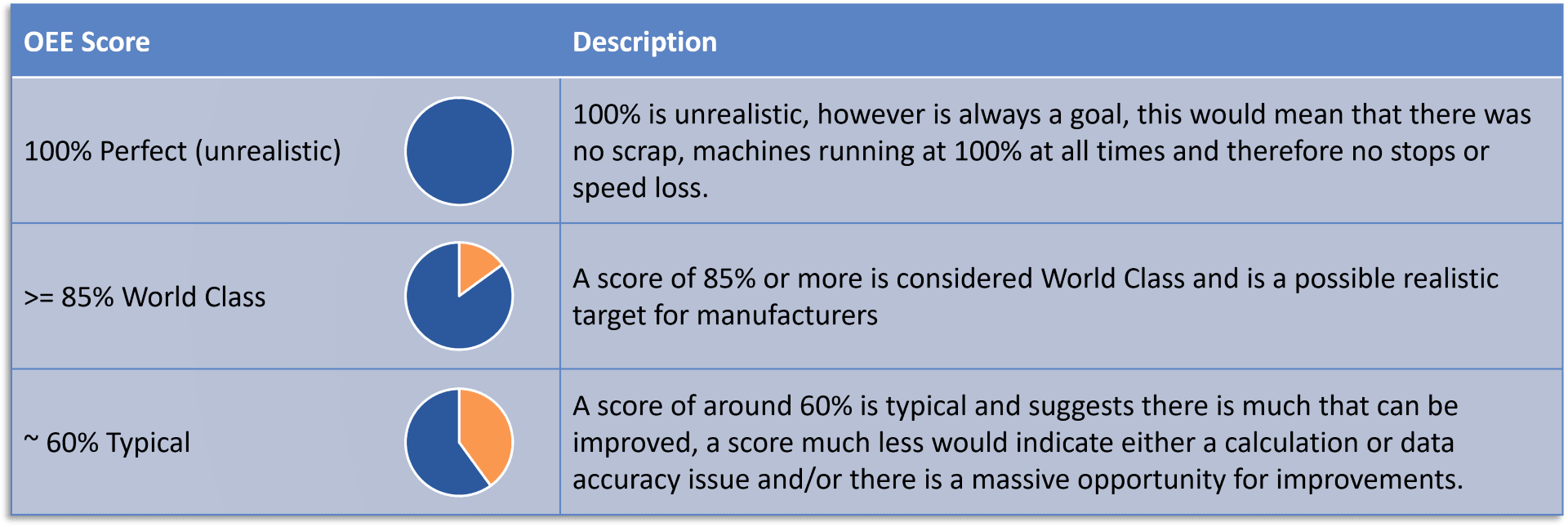
Typical vs World Class
It’s easy to see how difficult it can be to achieve a World Class score, given that 84% x 84% x 84% only equals an OEE score of 59% and therefore would be a “typical” OEE score.
An example of a world class OEE score would be 90% x 95% x 99% = 85% OEE
Accessing the Financial Impact of Improving Your OEE
Many General Managers understand OEE as some indicator that the shopfloor uses, and often complain about the maintenance team. However, for a manufacturer, the impact of OEE is across the entire company.
When you apply dollars to the OEE percentage is easy to see the financial impact. Below is a simplistic calculator that you can use to see the effects and the financial benefits you might achieve by improving your current OEE.
You will need an average sell and production cost over all the materials that you sell, in reality, the formula is more complex as you will have different OEE for different products and different markups, but at least you can see the impacts with a few numbers.
It should be noted that a 1% increase in OEE does not necessarily mean a 1% increase in Profits. Using our example figures a 2% increase in OEE would mean an increase of over 7% in Profits.
Replace the values that make sense for your business or just change the "Improved"OEE" to see the impact on the results and Net Profit.
Try our impact Calculator
How can you improve your OEE score?
You’ve seen with using our calculator how improving your OEE by just a few % can increase your profit so in practical terms where can you make changes on the shop floor? The six big traditional areas of losses sit in 3 areas; Availability; Performance and Quality.
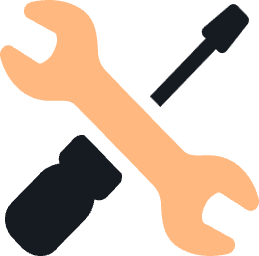
Availability
The first two of the Six Big Losses are about keeping your operations running as much as possible, maintenance of equipment, and scheduling of orders along with setups are key for this category.
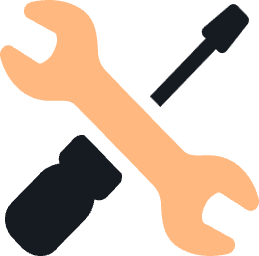
Big Loss #1: Equipment Failure (unplanned downtime)
Machine/Equipment breakdowns can be a significant source of unplanned downtime, to assist with improving your breakdowns the following are topics that need to be considered as part of your improvement process.
- Maintenance Plans –Ensure your machines/equipment are maintained to a level whereby unplanned breakdowns are reduced; this needs to be balanced with the non-productive downtime of machines during maintenance.
- Condition monitoring – Some machines may come with the ability to understand their condition, and others will require sensors to be attached to the equipment, Sensors can alert when a condition is met for example running HOT, or vibrations which might be an indication that lubrication needs addressing.
- Inspections – Having routine inspections of the machines, can often prevent breakdowns, and preventative measures can be put in place before an actual breakdown occurs.
An ERP such as SAP comes with the ability to help you manage the above topics. Understanding the patterns and reasons for these losses is key to helping to resolve them, having an MES (Manufacturing Execution System) such as SAP Digital Manufacturing enables the recording and analysis of downtime and is key to creating preventative actions that can be taken in the future to mitigate the risk of future events.
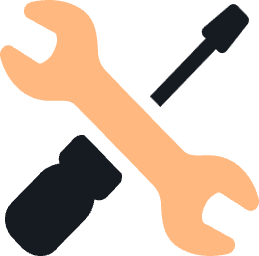
Big Loss #2: Setup and adjustments (planned downtime)
For most production lines there will always be some setup, adjustments and/or cleaning required, the good news is that this means there will be areas for improvement. Ensuring this is done correctly first time and efficiently is the key to success.
- Larger batches – the larger the batches the less setup and adjustment time that will be required, a key to this is in the planning and scheduling of your production.
- Optimising orders sequence – by correctly sequencing orders there may be the opportunity to reduce the setup/adjustments as some products may require a similar setup to others.
- Work Instructions - Optimised and easy-to-read work instructions will help ensure that the operators can execute the setup, adjustments and/or cleaning required correctly the first time and at an optimal efficiency.
An ERP and MES with solid planning and scheduling capability is key to being able to achieve the first two items, and an MES with the ability to store and display the correct work instructions for each order is essential for the 3rd item.
SAP ERP combined with SAP Digital Manufacturing provides a seamless planning and scheduling capability including the ability to schedule People, Resources and Tools for order execution. SAP Digital Manufacturing can store and display work instructions, including 3D models to help ensure the operators are best placed to execute the setup, adjustments and/or cleaning required for each order.
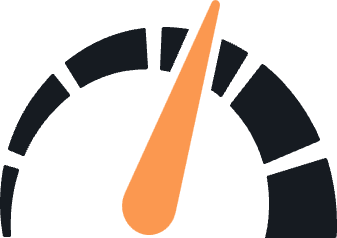
Performance
The next two Six Big losses are all about speed, ensuring you have realistic run rates for your machines and can keep the machines running consistently.
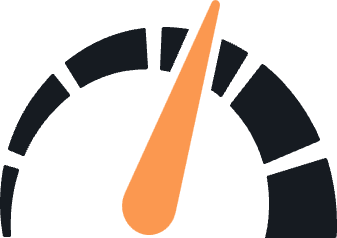
Big Loss #3: Idling and Minor Stops
Minor Stops can be hard to monitor and to some seem unimportant, however, a lot of machines have a ‘ramp-up time’ and therefore any minor stop has a bigger impact than expected. Idling can happen for example due to a lack of material to process as a downstream resource is having processing issues or there are internal transport issues within the plant.
Understanding the patterns and reasons for these losses is key to helping to resolve them, often it could be due to worn-out parts on a machine, or perhaps an issue with the packaging material that has been recently changed or the quality of the product being processed. An MES such as SAP Digital Manufacturing is capable of recording and reporting on these Minor Stops and Idling.
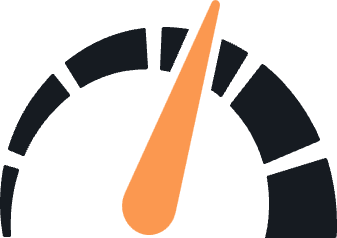
Big Loss #4: Reduced Speed
The impact of machines running at a reduced speed can be huge over a production run, and therefore it’s important to mitigate against these, the reasons for these can be much the same as with Big Loss #3 again understanding the reasons is key so preventative actions can be taken in the future.
- Incorrect setup – incorrect setups can be the cause of machines running at a reduced rate, ensuring that operators have good work instructions and are well trained is essential to helping mitigate this.
- Equipment– This can include worn-out equipment, lubrication issues, and dirt. Ensuring good maintenance plans/inspections, the operators need to respect and understand the equipment to get the best out of the equipment for the short- and long-term operation.
- Material – Either packaging or raw materials can impact the speed of processing, if there has been a change in the packaging the machines may need to be re-calibrated and off-spec raw materials can also impact processing speeds. A good change and quality control process along with systems can assist with this.
- Work Instructions – If the operators don’t have good instructions and training, this can lead to either machine operating issues and in discrete manufacturing an assembly process may take longer and increase the cycle times in a discrete operation.
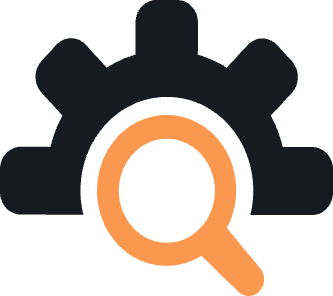
Quality
These final two Six Big losses are all about the Quality of the product/material you are producing. Quality is a make-or-break item and can lead to costly recalls if there are issues and they are not caught in time.
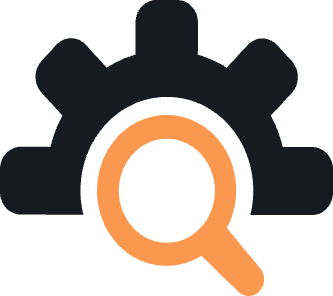
Big Loss #5: Process Defects
Once stable production is achieved, any rejects from that point forward would be counted here. The key here is to reduce production defects and ensuring they are spotted as soon as possible, as running for hours only to find at the end that the whole batch is defective is an operator worst nightmare.
- Use of AI - for defect detection can provide real-time alerts. SAP Digital Manufacturing comes with an AI Visual Inspection capability which can be trained to understand and detect defects.
- Regular Quality testing - can help save a batch and alert the operator of quality issues.
- Equipment Condition - can also play a part in rejects, so helping ensure your machines are inspected and maintained can assist with reducing these rejects.
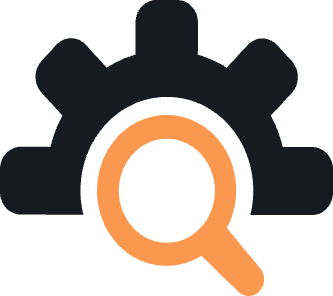
Big Loss #6: Reduced Yield
Startup Rejects are defective production produced from startup until stable production is achieved. They can occur after any equipment startup, however, are most commonly after a change in the setup.
If you are having problems with startup rejects then consider the following:
- Larger batches – the larger the batches the less setup and adjustments time that will be required, a key to this is in the planning and scheduling of your production.
- Optimising orders sequence – by correctly sequencing orders there may be the opportunity to reduce the setup/adjustments as some products may require a similar setup to others.
- Work Instructions - Optimised and easy-to-read work instructions will help ensure that the operators can execute the setup, adjustments and/or cleaning required correctly the first time and at optimal efficiency.
- Equipment condition - can also play a part in startup rejects, so helping ensure your machines are inspected and maintained can assist with reducing these rejects.
Summary
In summary, OEE is not just a score for production, it directly impacts the profitability of a manufacturing business. By improving your processes, user training and using tools like SAP Digital Manufacturing to help track and understand your OEE, you can take the required steps to improve your systems, processes, and people.