In the world of Manufacturing, the two acronyms - Manufacturing Operations Management (MOM) and Manufacturing Execution Systems (MES) - can be confusing, and people often use them interchangeably due to the overlap in functionality.
The simplest way to look at it is that the MOM is a restaurant General Manager, responsible for the overall management of the restaurant and ensuring that each section of the restaurant functions effectively and collaborates well together, whereas the MES is the Head Chef, overseeing the kitchen, which is responsible for producing the food.
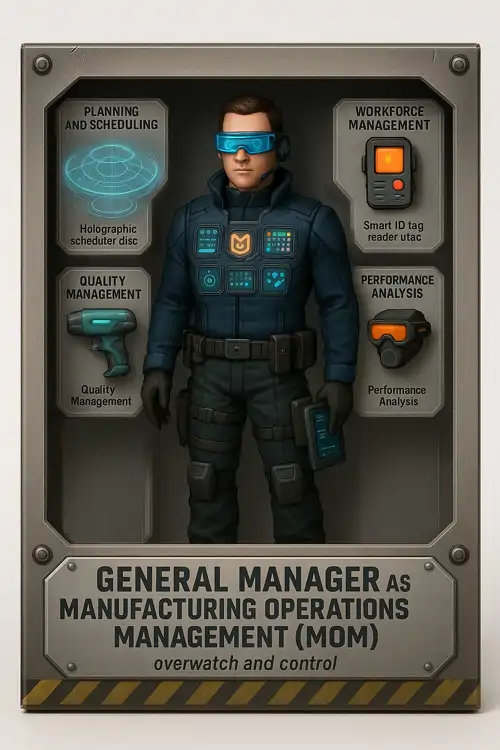
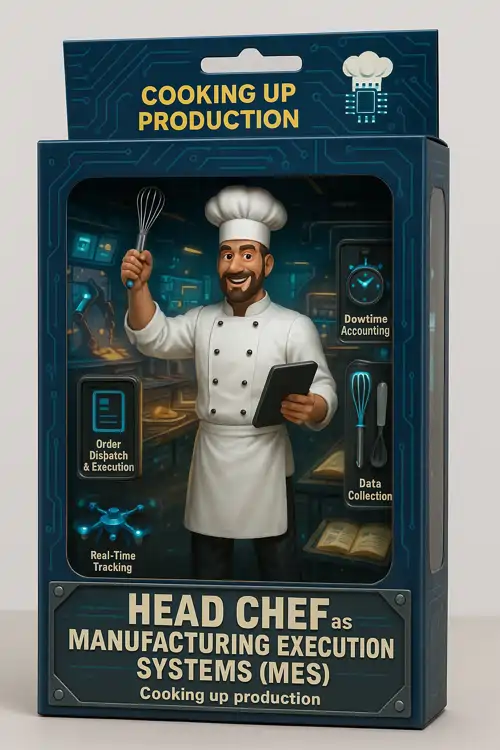
Given the above, you can now see that MOM systems are the strategic nerve centres of manufacturing and include functionality such as:
MOM - Planning and Scheduling
Involves creating a detailed plan and schedule for manufacturing activities, it must balance resources, production capacity, and customer demands to ensure timely delivery of products. It can also include long-term strategic planning and short-term operational scheduling to optimise workflow and reduce downtime.
MOM - Quality Management
Focuses on maintaining and improving product quality throughout the manufacturing lifecycle by performing inspections and implementing corrective actions if required. It helps ensure that products meet regulatory requirements and customer expectations.
MOM - Workforce Management
Deals with efficient management of human resources by planning shifts, assigning tasks, tracking performance, and ensuring compliance with laws and skills required to perform tasks, including operating machines.
MOM - Tools Management
Refers to the proper handling, tracking, scheduling, maintenance, and storage of tools and equipment used in manufacturing. This ensures tool availability, reduces wear and tear, and prevents production delays.
MOM - Performance Analysis
Involves monitoring and evaluating the production process using metrics such as efficiency, output, downtime, and defect rates, the standard KPI of Overall Equipment Effectiveness (OEE) is often used. This data-driven approach helps identify bottlenecks, optimise operations, and support continuous improvement initiatives within the manufacturing environment.
Where-as MES has a focus as below:
MES - Order dispatch/execution
MES - Real-time tracking
Involves continuously monitoring the status of machines, production orders, and materials as they move through the manufacturing process, allowing for immediate visibility into performance and potential issues. A live OEE score can be shown to the operators for the current production run and/or shift. This can then be used by Plant Managers and Operations to make informed decisions as required.
MES - Downtime Accounting
Is the method of recording and analysing machine and/or process stoppages, helping identify the causes of delays and improve equipment utilisation, this is a key requirement for OEE and continuous improvement.
MES - Data collection from operators and machines
Is the acquisition of production-related data, such as machine parameters, production counts, and operator inputs, either manually or automatically. This data supports real-time decision-making, quality control, and continuous improvement within the manufacturing environment.
Summary
In summary, the MES is responsible for ensuring products are made defect-free and at the right time with real-time reporting/visibility. With the MOM focusing on the entire production lifecycle, and not just execution.
In today's world of enterprise resource planning (ERP) there can also be an overlap of functionality of the MOM into the ERP, so these two systems must be well aligned and integrated to save the headaches of siloed systems and data. Having a fully integrated ERP, MOM & MES is key for the success of todays modern manufacturing. SAP ERP together with SAP Digital Manufacturing provides an integrated solution with all the key features of both MOM and MES that are key to successful manufacturing operations.