Cost pressures have been building for a decade in the Food and Beverage Industry. In the Sustaining Australia Food and Grocery Manufacturing 2030 Report from the Australian Food and Grocery Council they found that over the past ten years, Australian food manufacturers’ input prices have increased at an annual average rate of 4.1 per cent. This equates to an increase in food manufacturers’ primary input prices of 49 per cent from 2010 to 2020.
This is in addition to needing to meet growing customer expectations for speed of delivery, service quality, and personalisation, synchronise other parts of the business to respond instantly to changing demand and of course moving from spreadsheet-based systems to modern digital technologies.
It’s clear that businesses need more agile supply chain planning that delivers better visibility into supply and demand and the implications for manufacturing and logistics, leverage robust what-if scenarios to anticipate issues and plan ahead and real-time analytics for actionable insights.
This is in addition to needing to meet growing customer expectations for speed of delivery, service quality, and personalisation, synchronise other parts of the business to respond instantly to changing demand and of course moving from spreadsheet-based systems to modern digital technologies.
It’s clear that businesses need more agile supply chain planning that delivers better visibility into supply and demand and the implications for manufacturing and logistics, leverage robust what-if scenarios to anticipate issues and plan ahead and real-time analytics for actionable insights.
So how can integrated business planning help? It connects every part of the supply chain, which helps to deliver:
Smarter, lower inventories
Better visibility to anticipate & counter disruption
Greater production flexibility
Improved service delivery and higher customer satifisfaction
The Value is Clear
Integrated business planning can improve revenue, operating costs and asset utilisation/working capital
Revenue
Tangible Benefits* | % Impact |
---|---|
Top line revenue growth | 1-2% |
In-stock % improvement | 20-30% |
Service level increase | 5-10% |
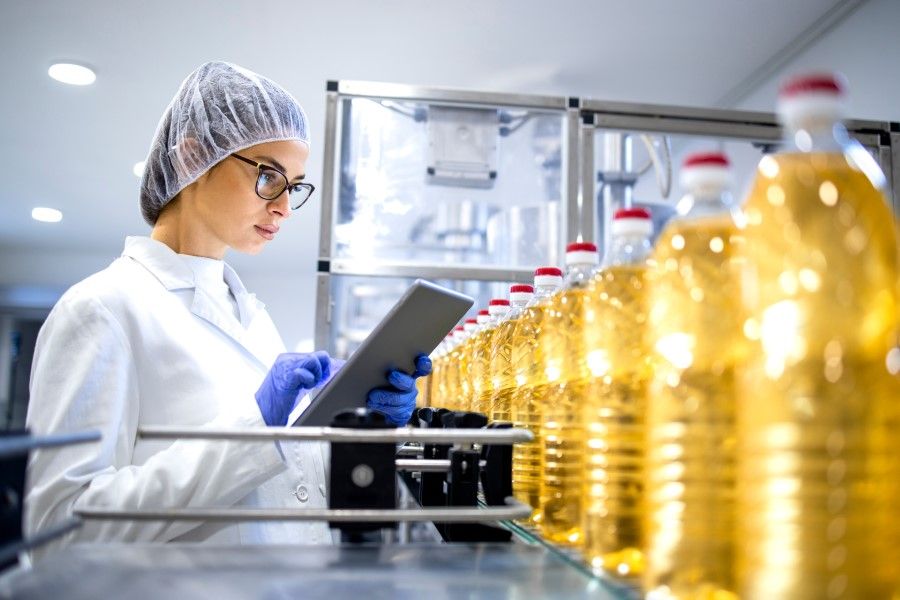
Operating cost
Tangible Benefits* | % Impact |
---|---|
Improved planner productivity | 20-30% |
Order fulfillment lead time reduction | 10-20% |
Inventory carrying cost reduction | 5-10% |
Asset Utilisation/Working capital
Tangible Benefits* | % Impact |
---|---|
Reduction in inventory levels | 5-15% |
Inventory turns increase | 5-10% |
Cash-to-Cash cycle time reduction | 5-10% |
* IBM, Aberdeen & Gartner Case Studies & Benchmarks from SAP Value Engineering
What does SAP IBP offer?
- Demand management: SAP IBP integrates historical data, market trends, and advanced predictive analytics so that you can generate more accurate demand forecasts.
- Response and supply planning: SAP IBP takes capacity constraints, lead times, and inventory levels into account so that you can optimise production and distribution plans and more efficiently meet customer demands.
- Inventory management: SAP IBP helps you maintain optimal inventory levels by balancing the trade-offs between carrying costs, stockouts, and service levels.
- Sales and operations planning: SAP IBP provides a unified platform for collaborative planning, allowing different departments to align on strategic goals and operational plans.
- Demand-driven replenishment: SAP IBP supports DDMRP for strategically positioning inventory buffers in the supply chain to absorb variability and uncertainty.
- Supply chain control tower: SAP IBP supports the real-time supply chain visibility and enhanced analytics you need to quickly respond to changing market conditions and customer requirements.
Who uses SAP IBP?
More than 1000 companies worldwide use SAP BTP to streamline supply chain and planning processes. Ranging from large multinational corporations to medium-sized enterprises, these companies span a wide range of industries, including manufacturing, retail, consumer goods, pharmaceuticals, automotive, aerospace, and many others. Some of the key users of SAP IBP include:
- Supply Chain Managers: They use SAP IBP to optimise supply chain processes, improve visibility, and monitor and control inventory levels.
- Demand Planners: They use SAP IBP to forecast customer demand accurately, align supply with demand, and improve overall customer satisfaction.
- Sales and Operations Planners: They use SAP IBP to align sales, marketing, and operations teams to execute integrated business plans and achieve financial targets.
- Inventory Managers: They use SAP IBP to optimise inventory levels, minimise carrying costs, and improve working capital efficiency.
- Executives and Decision-Makers: They use SAP IBP to gain insights into the overall health of the business, make data-driven decisions, and drive strategic initiatives.
Summary
For Food and Beverage Manufacturers as well as other manufacturers who are under cost pressures, the value of IBP is clear, it allows them to leverage their people and their data to make better decisions. It links strategic and operational supply chain planning with real-time visibility, response and execution all in one place. Speed responsiveness and staying ahead of change.
Access the full report here - Sustaining Australia: Food and Grocery Manufacturing 2030
Access the full report here - Sustaining Australia: Food and Grocery Manufacturing 2030
Contact us to find out more
Speak to us about how our team can assist you.