Manufacturers have spent the past four years essentially firefighting the pandemic and its aftermath. Unsurprisingly, everyone is hoping for some semblance of normalcy to endeavour to continue to rebalance business in 2024.
Manufacturers will need to accelerate investments to protect long-term profitability by broadening their smart manufacturing capabilities with digital transformations. While digital transformation offers many benefits for the manufacturing sector, it also comes with the potential to add to cybersecurity risks if you don't select a certified and proven solution against attacks.
In a recent study, more than half of surveyed manufacturing companies said they were targeted by ransomware, with nearly seven out of 10 of these attacks resulting in malicious data encryption. (“Insights from ‘The state of ransomware in manufacturing and production 2023’,” Sophos, June 21, 2023)
30%
of extortion targeted manufacturing *
41%
of attacks used phishing *
6%
of attacks were due to business email compromise*
Embracing the Future of Manufacturing
Manufacturing facilities are now at a tipping point of smart factory adoption, moving from occasional or sporadic implementations of smart equipment and software to more full-fledged solutions which can take advantage of today's technology.
Why? There are a couple of reasons:
- As older equipment continues to be phased out, newer machines come equipped with onboard sensors and monitoring tools that can be integrated.
- Manufacturers will be increasingly motivated to implement smart technology to keep pace with competitors who are already seeing the benefits.
On top of this, the costs of aftermarket sensors and other smart factory software and equipment continue to drop, while the business benefits increase.
Trend 1: The Role of AI in Operations
Todays manufacturing equipment with sensors and traditional SCADA and PLCs yields an abundance of data, encompassing process and performance parameters. To match that new MES and ERP Solutions can extract valuable insights from this data, which is key to optimising production, scheduling maintenance, and effectively managing assets. Quicker and improved decision-making is a key outcome of this ability, as manual data analysis is time-intensive while standard computer software often falls short in recognizing trends and drawing logical conclusions.
AI, a pivotal player in the realm of manufacturing trends, offers a solution to the challenge of quickly analysing large datasets and deriving actionable insights. The AI revolutionises multiple facets of manufacturing operations. It spans inventory management, supply chain visibility, cost reduction in warehousing, and quality control. Additionally, AI’s application in predictive maintenance ensures that manufacturing companies operate with minimal or zero unplanned shutdowns.
In 2024 we will continue to see shopfloor AI utilised for things like quality inspections. AI-based visual inspection for defect detection is a feature that will continue to benefit a range of manufacturers.
Trend 2: Meeting increased demand with a possible decreased labour force
With demand for manufactured goods continuing to grow, manufacturers are leaving money on the table if they are not able to increase capacity and throughput to fulfill these needs. This requires a top-to-bottom evaluation of all processes, identifying ways to increase efficiency and support the workforce while bridging the skills gap and providing cutting-edge technical training to meet today’s needs. Some of these trends build on those with which you may be familiar from past years, and some are new as a result of today’s unique challenges.
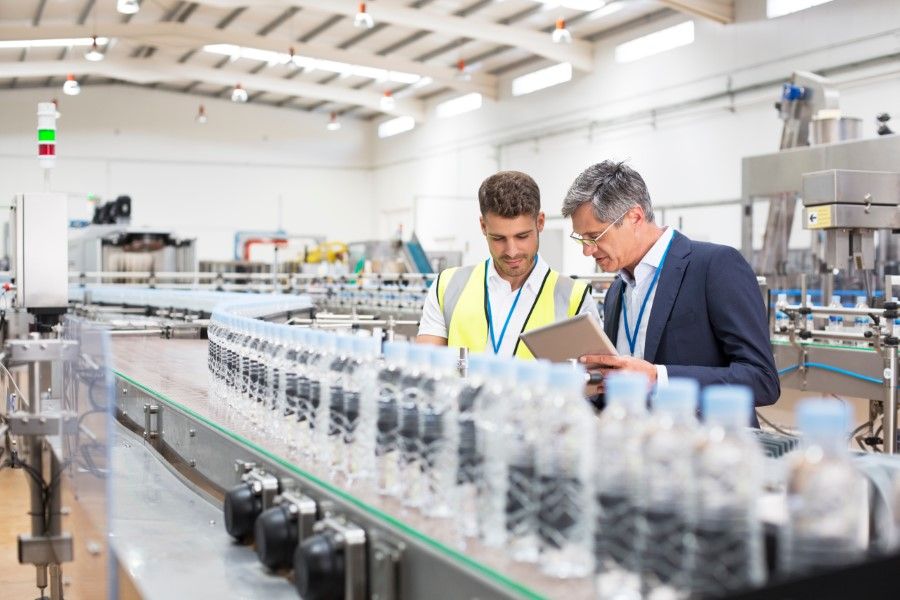
To address these concerns manufacturers should be considering strategies such as Automation and Robotics, Advanced Manufacturing Technologies, Cross-Training Employees, Outsourcing and Partnerships, Employee Engagement and Retention as well as Investing in Training and Development.
Manufacturers need to assess their specific situation and industry requirements to determine the most effective combination of these strategies for their circumstances. Additionally, staying abreast of technological advancements and industry best practices is crucial for adapting to changing market conditions.
Trend 3: IIoT (Industrial Internet of Things)
Integration of interconnected equipment, sensors, devices, and instruments throughout the manufacturing process is enabled by the Industrial Internet of Things. These devices provide real-time data and connectivity, allowing manufacturers to monitor and control their operations with advanced MES solutions, like SAP Digital Manufacturing, the data from IIoT unlocks advanced solutions for manufacturers like predictive maintenance.
Continuing in 2024 IIoT technologies will enable better traceability of products throughout the supply chain, which is crucial for compliance, quality control, and managing recalls if necessary.
IIoT can enhance efficiency, reduce costs, and improve worker safety by streamlining processes and asset management. Removing the manual recording and paper from the shopfloor will help revolutionise manufacturing, making it more data-driven and agile, ultimately leading to increased productivity and competitiveness in the industry.
Continued adoption of IIoT in manufacturing in 2024 will bring about significant improvements in operational efficiency, quality control, cost reduction, supply chain optimisation, safety, innovation, and customer satisfaction.
Trend 4: Cloud Computing
Manufacturers will continue to utilise cloud computing to host IT infrastructure in remote data centres, to store, manage, and process data and applications.
These cloud solutions mitigate the need for expensive IT infrastructure costs and maintenance. One key benefit of this approach is enhanced flexibility and scalability, allowing for rapid adjustments in response to changing production demands. This flexibility improves efficiency and reduces costs.
Providers such as SAP have cloud data centres that are certified and provide sophisticated cyber security protection, thus addressing one of the key risks for digital transformation projects for manufacturers. On top of this, the data centres adhere to industry-specific compliance standards and certifications, making it easier for manufacturers to meet regulatory requirements and ensure data integrity. With access to Industry Best Practices these cloud solutions can simplify and accelerate business processes.
To address possible downtime some solutions, have an edge component, which can be used to keep the production running in the event of scheduled or unscheduled downtime of the cloud or the internet connection.
In summary, cloud computing in manufacturing will continue to provide a wide range of benefits, including cost savings, scalability, improved collaboration, enhanced data management, flexibility, security, and support for innovation with the risk of software downtime impacting production mitigated by edge computing. Leveraging cloud services manufacturers will continue to optimise their operations and stay competitive in an ever-evolving industry landscape.
Trend 5: Big Data & Analytics
Tightly coupled to IIoT and all the data associated with it is Big Data and Analytics. As highlighted within the IIoT trend above data is key to many improvements within manufacturing.
Production efficiency will be improved with analytics identifying inefficiencies and bottlenecks, quality control analysing data from sensors and production systems helping with the early detection of defects, reducing waste, and ultimately ensuring higher overall product quality. Reduced downtime can also be achieved by analysing data from sensors and machinery with predictive analytics forecasting when equipment is likely to fail. Real-time monitoring provides real-time insights into the manufacturing operations, allowing for quick decision-making and rapid response to changes or issues, lastly, KPI tracking can be monitored and analysed to track the overall performance of manufacturing processes and identify areas for improvement.
We are seeing advanced MES solutions such as SAP Digital Manufacturing combining data from many plants and offering the ability to compare the differing plants, providing insights into how and possibly why they achieve different production results. These insights lead to targeted improvements in various aspects of operations which positively impact the overall performance.
Valuable insights from the vast amount of data generated in manufacturers' own operations will enable continuous improvement and innovation. Leveraging big data and analytics in manufacturing will contribute to operational excellence, improved product quality, cost savings, and importantly enhanced overall competitiveness.
Summary
In summary, Manufacturers will continue to need to work smarter, leveraging technology and their own data to protect long-term profitability. Investments will further enable manufacturing capabilities with digital transformations, while at least one eye needs to be kept on the possible risks associated with the increasing risk of cyber threats.
There are plenty of opportunities for Manufacturers to adopt smart factory solutions, with AI, IIoT, cloud computing with the key enablers being big data and analytics. Embracing the future of manufacturing by taking advantage of today’s technology will continue to contribute to protecting the long-term profitability and success of operations.